Well much has happened since my last blog post update. And, as I’m writing this, I’m realizing just how helpful keeping a daily log would have assisted me with this process right about now! I could probably write a novel detailing all of the adventures and lessons I’ve experienced these past 6 weeks, but I will spare whoever is reading this the word count.
After our two week boot camp, we dove into our internships. I am working as a Sustaining Engineer at ICU Medical, a global medical device company that specializes in IV medication delivery. Their range of products spans from blood sample systems to customized infusion equipment to catheters and advanced sensors. However, their most well-known work involves their PCA vial and Plum 360 products. I have had the opportunity to work with an amazing team of engineers to do a variety of projects focused on these two areas.
At first, like most of the students, I was pitched a singular project that would span a full summer to complete. But after preliminary talks with my supervisor, we came up with a work schedule that was more my style: lots of mini hands-on projects I could work on in parallel with the main one. So, in the past 4 weeks I’ve started on 5 different projects that mostly keep me busy. I think my boss might get tired of my “More Work Please?” emails! But I’ve found I work best switching between tasks so I don’t get bored- and bored = unproductive. So, as I like to remind him: hey, I’m free labor, you might as well use me! My team has been so incredible letting me jump right into projects and letting me run with things. I’m actually designing my own testing, writing my own protocols and performing my own assessments.
Here’s a bit about what I’ve been up to at work. My main project is investigating and designing a test protocol to insource production of a key component to one of our machines. Bringing back production to Costa Rica would vastly reduce shipping cost and time as well as provide us agency on verifying testing and usability of our samples in real-time to prevent latent delays in our production line. I’ll be honest, when I heard this systems-level operation project, I didn’t exactly think of engineering- at least not the equations and gears and motors I get excited about. This project involves more contact making, quoting, systems mapping and technical writing than engineer-ing. However, this big-picture project is a great opportunity to learn how a global company operates, how they implement procedures and the workflow of integrating across departments to develop a single product out of many intricate components. This business proposal is a new perspective that I think engineers are rarely privy to, so in addition to the immediate hands-on component work, I can visualize the abstract system-wide company work. They are the opposite sides of engineering but I think both are essential to successful medical device commercialization.
One of the downsides to working at a global company level- is that you are at the mercy of the schedules of the people who run it. This has afforded me the chance to spearhead other projects as I wait for updates or responses to carry forward.
Without getting too much into the proprietary technology I work with, let me just say this: it is very fascinating and very intricate how IV medication infusion pumps work. A lot of Sustaining Engineering is identifying failures and reverse-engineering to perform root-cause analysis through extensive testing. That’s where we get to be creative. In one of the production lots, noticeable cracks in the rear plates were discovered. I was tasked with exposing these plates through rigorous testing to determine if a) those with cracks will intensify after loading, b) if the presence of cracks will necessitate failure, and c) will those without cracks develop them after loading. This was a simple enough task that required about 200 cycles of loading. So at this point, I would like to count myself a master of the assembly process.
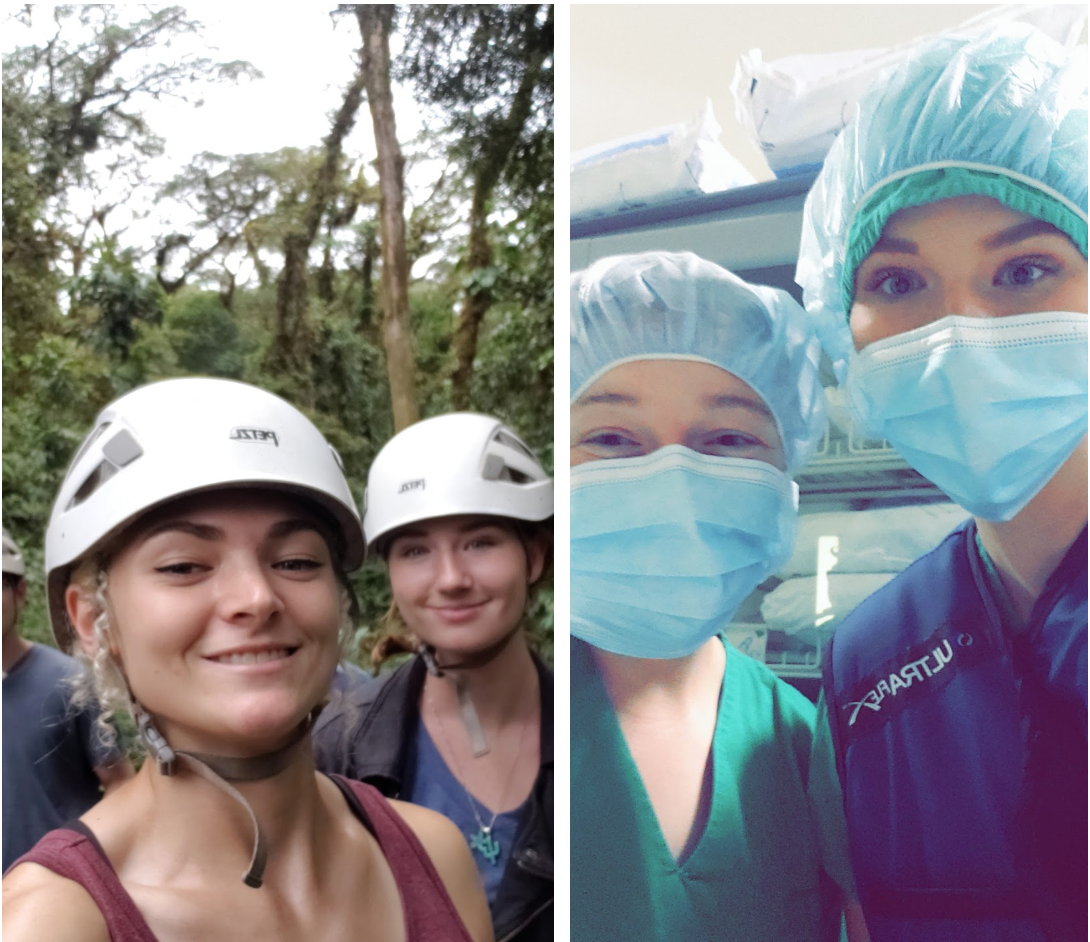
Another project involves the failure of a plunger to activate an optical sensor at the appropriate number of steps. In some cases, it would prematurely trigger the sensor or take too long. In order to assess the failure, we performed a stack up equation in which we retrieved all of the specification dimensions and formulated an equation to measure the acceptable gap tolerance between components. I looked at a lot of complicated schematics and took a turn at de-assembling a few spare mechanisms I was given to play around with. Suffice to say, there are many tiny springs and brackets that are lost on my carpet somewhere leaving a graveyard of separated parts on my shelf. But this decomposed view is a great way to see how each part works in conjunction with another to perform a complex set of tasks that are responsible for delivering very precise levels of life-sustaining medications. It is funny to think about how a handful of small screws, plastic and motors are responsible for keeping a patient alive.
This internship has been wonderful; I adore my coworkers and have greatly enjoyed my projects. But I’m sure by now, you have lost interest in reading more about my work- so here is your reprieve:
This summer, in addition to work I have been fortunate enough to leave the office and explore more of Costa Rica. One of our more recent trips took us to the must-see town of Monte Verde.
Learn more about our one-year, full-time Master of Bioengineering in Global Medical Innovation.